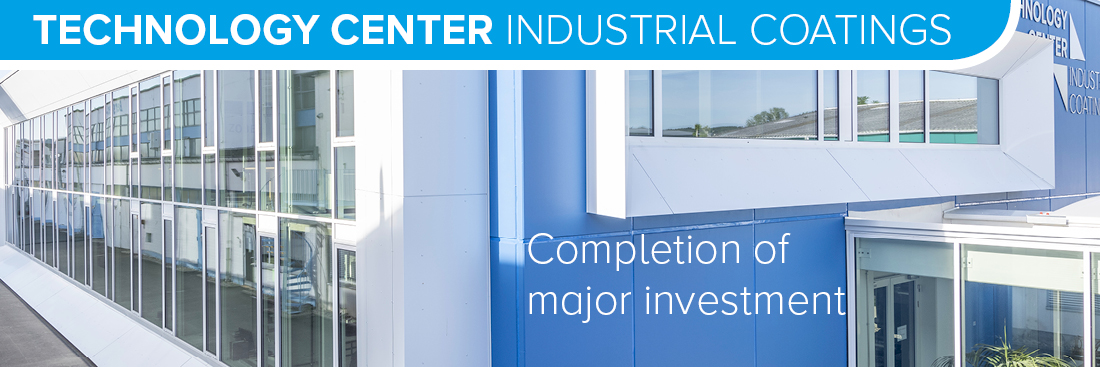
Grand Opening of the Major Investment at Berger-Seidle
The coating specialist Berger invests in new technology center, new production logistic halls and production lines – Minister of State Dr. Wissing is Special Guest
Almond blossom time and sunshine in the Palatinate vineyards. A wonderful setting for the opening of the new TechnologyCenter at the coating specialist Berger in Grünstadt. As part of the official opening with around 200 employees and guests from politics, business and business partners, the official start of the new buildings took place on March 22, 2019. As a keynote speaker and guest of honor, Dr. Volker Wissing, Deputy Prime Minister and Minister of State for the Economy, present at the location – along with many other guests of honor from local and state politics as well as the economy. Thomas M. Adam (managing partner of the Berger Group) and architect Frank Wolf (P4 architect Frankenthal), among others, presented the framework, purpose and design of the buildings in a relaxed, festive atmosphere. Afterwards, the guests were able to visit the buildings on guided tours after a cozy get-together.
The heart of the new building is the large, modern TechnologyCenter IndustrialCoatings. This new, two-level building with a floor space of almost 1000 square meters significantly expands the capacities in the area of development and application technology. Specifically, new development laboratories were created, a large technical center for testing and presenting coating systems, training rooms, testing technology rooms and a workshop for the preparation and storage of sample parts.
With the new TechnologyCenter, Berger is significantly expanding the capacities of the relevant development and test processes. The level of technology is unique. New application systems, air-conditioned drying and coating zones, additional test equipment and machines and much more expand the existing equipment to a state-of-the-art level. This also includes all relevant coating application processes for spraying by air, airless, airmix, electrostatic or Vacumat processes as well rolling, flooding or dipping. The same applies to the drying options of air, oven and UV drying. Climate chambers comprehensively cover the global air drying conditions of the four extreme climates. A highlight here is a new robotic test coating system.
The building is used by all company segments window coatings (Berger-Zobel), industrial coatings (Berger-Lacke) and parquet coatings (Berger-Seidle). It serves as a development, test and customer training center. The architecture of the TechnologyCenter equally reflects innovative strength, quality, modernity and practical relevance.
Another part of the overall investment measure is the expansion of the production area by two new storage and logistics halls. Space for a new locksmith shop, new storage areas for raw materials and packaging as well as various tanks for water-based binder systems with a capacity of up to 30,000 liters each was created on a floor space of almost 400 square meters. On a further almost 600 square meters, a new, additional shipping area was created, which significantly expanded the previous shipping capacities, equipped with four truck docking stations. The significantly increased shipping volumes, especially in the area of large shipments to globally distributed customers in overseas containers and jumbo trucks, made this expansion necessary in the straightening and shipping area. At the same time, the production area was expanded and partially rebuilt. With new systems, not only did additional capacities emerge, but also the most modern and partially automated processes.
The total investment is several million euros. The Berger Group has more spacious buffer areas on the company premises at the Grünstadt site for further, sustainable corporate development at the site.
The number of employees has recently increased as part of the takeover of Zobel-Chemie from Worms at the Grünstadt location and is now around 110 employees. The company is planning a further slight increase in the number of employees in 2019 and is assuming a positive sales trend. Further investments are already planned for 2020 and 2021, including in internal logistics.
With these expansions and optimizations, the company is not only preparing itself for further growth opportunities, but also for possible global economic crisis situations. Both are an integral part of the sustainable risk management of corporate management in order to be able to offer maximum security and a lot of perspective not only to the company but also to the employees.